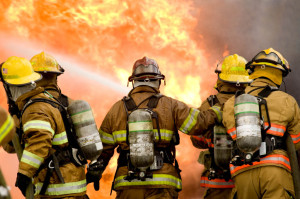
Improving textile product performance and safety requires collaboration.
The process of revising standards can provoke some lively discussions and detailed decisions. The standards (some enforceable and some voluntary) guide material and product manufacturers through the complex world of creating safe and functional products.
Hundreds of standards affect the specialty textiles industry, and keeping up with them is time consuming and expensive—and even confusing, at times. As representatives from the industry work to revise existing standards they also share a second goal: to create a more streamlined approach.
Challenges for labs
“As a test lab scientist, I have to deal with numerous standards for products,” says Rob Kinsler, chief, technical operations for HP White Laboratory Inc. in Street, Md. “Each one is slightly different. It gets expensive for me to have to keep purchasing a new standard every time it gets updated just to change a numbering scheme or some other typo.”
Kinsler is a physical scientist for the laboratory that conducts independent ballistics testing for articles including body armor, helmets, vehicle armor and structural armor. He also works on an ASTM (American Society of the International Association for Testing and Materials) committee: ASTM D13 on Textiles.
“From a standards developer viewpoint, I understand the issue with writing a standard where one already exists,” Kinsler says. “In several ASTM meetings I’ve been at recently, the groups have voted to just point to currently existing standards rather than drafting new ones. Several of us are also aware that without ‘teeth’ standards are being written for no reason. If no one has a requirement that a standard be followed, most people don’t pay attention to it.”
Seeing double
For years, the issue of duplicate standards has been a hot topic in the standards community. ANSI (the American National Standards Institute) serves as coordinator of the U.S. private sector, voluntary standardization system, and has for more than 90 years. For the more than 220 ANSI-accredited standards developers—including ASTM International, Underwriters Laboratories Inc., NFPA International, ASME International, ASHRAE, CSA America Inc. and NSF International—duplicate standards continue to be a problem.
To help address the issues, in 2012 ANSI launched an initiative to redevelop NSSN, its search engine for standards. With support from NIST (the National Institute of Standards and Technology) ANSI reworked NSSN to make it easier for stakeholders and standards developing organizations (SDOs) to have access to information that may help to avoid the creation of conflicting or duplicative standards, according to ANSI’s July 2012 workshop summary report.
While the updated search engine is a step in the right direction, standards committee members are still left to hammer out the details of new and revised standards—and to move in the direction of collaboration.
One product, multiple standards
One element of collaboration has to do with working with different manufacturers of the materials that make up the final product. In the case of protective clothing and equipment, that means making sure the performance standards are well coordinated so that all pieces of the end product perform in concert “because a lot of the standards tend to only address one component of the end product,” says Don Thompson, associate director of the Textile Protection and Comfort Center at North Carolina State University in Raleigh, N.C. Thompson also works on the Correlating Committee for the clothing department for NFPA (National Fire Protection Association).
According to NFPA website information, the Correlating Committee reviews the standards related to protective clothing and equipment for the association that “develops, publishes, and disseminates more than 300 consensus codes and standards intended to minimize the possibility and effects of fire and other risks.”
Thompson says a big part of the committee’s work right now focuses on harmonizing between the different standards for equipment and clothing that are used together.
“For example, the face piece of a respirator is made from entirely different materials than the garment itself,” he says. “We’re trying to get those to work together to make sure the protection is consistent between them—so the face piece doesn’t fail before the garment does. The truth is, it’s a complicated thing because the plastic materials available for face pieces don’t have the same characteristics as Kevlar® and Nomex®.”
Raw materials vs. end products
Testing can occur at two levels: raw materials and end products. Some manufacturers test both raw materials and end products; others test only the final product. There are pros and cons for both, says Seemanta Mitra, senior director, global account management and global softlines for Intertek, a global company that provides quality assurance for multiple industries.
“In the first case, the testing cost is higher as two-stage testing is performed: development stage testing and final product testing. However, it provides a higher degree of assurance on the quality of the product,” Mitra says. “In the second case, the testing cost is lower because only the final product testing is performed, but the manufacturer or retailer runs the risk of discovering any testing failure(s) very late in the process.”
“We’ve begun to move from only testing materials toward creating ensemble level specs,” Thompson says. “Because what really counts is how [the end products] work for the human. That would mean a test of a material may be a prerequisite but it may not be adequate to address how the product performs on the human.”
Thompson points out that it’s vital to include a significant number of end users on standards committees, because they will be most affected by how well the product(s) perform.
Innovation
Streamlining existing standards is challenge enough, but with new products and materials being developed, there is often the need for new standards as well. Because it takes time to develop new standards, often innovations are ready to be rolled out before the appropriate standard is created.
“On more than one occasion I have had to deal with an innovation that doesn’t fit neatly into the standard,” Kinsler says. “At those times, we have followed the intent of the standard and documented any subtle changes that were needed. Generally, when sitting on standards committees, I try to think outside the box—to write the standard for future innovations. Fortunately, most standards organizations have mechanisms in place to allow for standards to be updated when new innovations appear.”
Mitra points out that another option is for testing laboratories to assist manufacturers to create an “in-house” test standard for innovations when there is no existing standard that applies.
“Some of those in-house test standards may eventually become national test standards adopted by organizations such as ASTM,” Mitra says.
Reaching consensus
The bottom line is that streamlining standards will likely be an ongoing challenge, because it is the nature of this industry to change and innovate. So, the need for new standards and standards committees will persist as well.
“It all comes through consensus,” Thompson says. “And believe me, there are some battles over things, because sometimes requirement cuts against somebody’s technologies or equipment they’ve already got, or practices they already have. But I think everybody involved has their heart in the right place and is trying to develop the best standards possible.”
Sigrid Tornquist is a St. Paul, Minn.-based freelance writer and editor.