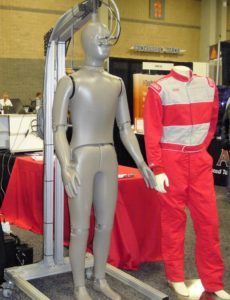
Most of us are familiar with the basics of textile testing for comfort, aesthetics and durability in apparel textiles. But the development of textiles for technical and industrial end uses requires an understanding of existing and new criteria for measuring and evaluating textile attributes.
These and other aspects of textile testing were included in the Advanced Textiles Conference Testing Track at IFAI Expo, held in Charlotte, N.C., in October. Sponsored by North Carolina State University (NCSU) College of Textiles and IFAI Advanced Textiles Source, the testing program included lab time at a number of exhibitors in the Expo’s Testing Demo Zone, including NCSU, the International Antimicrobial Council, FITI Testing & Research Institute, and the Hohenstein Institute.
Completion of the testing track earned a certificate from NCSU, to be used as credit toward the NCSU Textile Technology Certificate Program.
Kent Hester, director of student and career services at NCSU College of Textiles, reminded us that the NCSU facility is the only remaining college of textiles in the U.S. where technical, business and creative aspects of textiles are all included in the curriculum. Hester reported that an increasing number of textile and apparel companies, as well as retailers, have been calling the college looking to “replenish the pipeline” as current management moves toward retiring.
Why test?
The annual cost of testing, inspecting and certifying textiles is anticipated to reach $7.22 million by 2020, according to a report posted by research firm MarketsandMarkets. Driven by increases in trade, the introduction of new standards and regulations, and innovations in textile technology, global textile testing could see a CAGR of 4.6 percent between 2015 and 2020.
As textile technologies and performance claims grow in number and complexity, retailers, as well as consumers, want to be assured that a product is and does what it promises.
Governments and regulatory groups are becoming increasingly involved, particularly regarding claims such as flammability, odor control, durable water repellency, thermal regulation and provenance.
“The expense of testing is not at all costly when compared to the cost of returned merchandise and dissatisfied customers,” insisted Dr. Jan Pegram Ballard of NCSU College of Textiles. Pegram’s review of test methods for fiber, yarn and fabric stressed the need for the standardization of test procedures, equipment calibration, specimen conditioning and the training of personnel.
Thermal testing in the real world
Thermal testing is especially critical in safety apparel and other textiles products that protect military personnel, first responders and industrial workers. Dr. Emiel DenHartog of the Center for Research on Textile Protection and Comfort (TPAC) at NCSU spoke to the inadequacies of existing tests in assessing comfort as well as protection in the workplace.
“There are currently huge discussions in the fire-fighting community about assessment,” DenHartog said. While sweating hot plates and manikins measure the heat loss and evaporative resistance of clothing, they are unable to predict the range of human responses in the real world, including core and skin temperature and sweating rate while working, he explained.
DenHartog referenced the approach of ThermoAnalytics, whose software utilizes transient analysis (as opposed to static measurements) to predict the response to thermal challenges.
DenHartog also pointed out the difference in measuring moisture management, or wicking, as opposed to measuring thermal comfort. It is the process of evaporation that makes one feel cooler. “In a sensorial way, dry is more comfortable—but it is not cooler,” he explained.
Textile properties can be measured and substantiated, he concluded, but they are not necessarily relevant to what happens in the field. Testing should include ergonomics and task performance; and protective systems must balance performance and comfort. “It is not hard to protect people—but we have to enable them to perform their jobs,” said DenHartog.
Testing the fabrics of the future
Standardized testing is also being challenged by new fibers, technologies and products, such as electronic textiles, where appropriate testing protocol may not exist. Conductive materials can be applied to textiles in a number of ways, including printing, embroidery and conductive filaments or coated fibers. But not all of them stand up to consumer wear and home laundering, explained Dr. Jesse Jur of NCSU’s department of textile engineering, chemistry and science.
A NCSU student team, led by Jur and his colleague Dr. Russell Gorga and sponsored by Hanesbrands, tackled the development of a biometrics feedback shirt intended to prevent heat-related injury by monitoring hydration levels and internal temperatures.
Conductive (Ag) inks were screen printed on the knitted garment to create the circuits for flexible sensors; but stress/strain testing showed that the circuits failed when the garment was stretched. Creating a sandwich for the Ag ink with TPU, which was then laminated to the textile, improved the resistance of the circuitry when stretched. However, the project samples failed to perform after two standard washings, indicating the need for more robust conductive materials.
According to Jur, a number of organizations are working towards establishing testing standards for smart textiles, including ASTM’s subcommittee on smart textiles, and AATCC’s exploration of a wash test method for electronics. The impact of wearing electronics on the body also needs to be tested, he added.
Jur and Gorga gave other examples of the importance of testing in the development of new products, and the need to clarify design criteria and constraints in order to develop testing protocol. For example, the reinvention of individual finger cuff sports grips for athletes required the development of a coefficient of friction test, while a cooling vest for confined workers was tested via a heating pad manikin, which recorded the wattage consumed by the heating pad while wearing the vest. The wattage was measured separately on the front and back of the manikin, effectively measuring the cooling capacity of the vest in different zones. “Testing and evaluation are the most critical parts of the design process,” reiterated Gorga.
Solutions from Expo exhibitors
The Hohenstein Institute focuses on testing and certifying the unique functional characteristics of new textile products, assisting product developers by “thinking out of the box,” according to Dr. Jan Beringer, head of development, function and care at the organization. For example, the institute developed a thermo-physiological test using a climate-controlled cabinet to simulate and measure how a body emits heat and sweat.
The counterfeiting of textiles and the substitution of inferior materials within the manufacturing process to save costs is another growing issue. Applied DNA Sciences (ADNAS) uses their Signature® T DNA markers to tag fibers at the source, enabling brands to test and track their products through the supply chain, assuring their provenance.
While the challenges of managing textile testing aren’t going away any time soon, Texbase Inc., a software company, offers systems that capture, analyze and report physical test data, making it easier for brands to be compliant. Texbase materials and testing management software can also be integrated with PLM systems such as Gerber’s YuniquePLM™.
The claims made by many of the latest textiles might seem to be a leap of faith, but the testing industry is working hard to assess and certify the comfort, safety and performance of these products, ensuring that the development process is sound and that consumers are getting value for money.
Debra Cobb is a freelance writer with extensive experience in the textiles industry. She is a frequent contributor to Advanced Textiles Source.