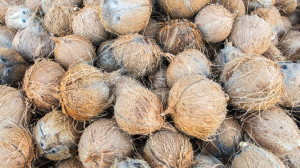
A dictionary definition of sustainability says that it’s an ability to last or continue for a long time. In other words, it’s all about conserving resources for the future, while judicially utilizing them in the present time. Based on this, sustainability can be grouped into two categories: focus on the reduced use of materials (reduce, reuse and recycle (the 3Rs), and focus on practical aspects such as environmental friendliness, energy efficiency and economic viability (the 3Es). From a practical point of view for industries to embrace sustainability it has to be built on both the 3Rs and 3Es.
Among the factors that led to the slowdown of the conventional textile industry in the West were unsustainable scenarios with regard to environmental issues and economic aspects. To overcome this, the U.S. and European Union (EU) countries have focused their attention on industrial textiles, which are generally high specialized. These textiles are geared towards improving human life and protecting the environment. This specialized sector manufactures products such as medical textiles, infrastructural fibrous materials, military textiles, and sports applications.
A majority of these use synthetic materials and their main attribute is functionality. However, such attributes can also be achieved using natural materials by enhancing their characteristics. The next phase of the industrial textiles industry should focus on sustainability, and that will, of course, take into account the 3Rs and 3Es.
Sustainable raw materials
Currently, the specialty textiles industry is experimenting with the use of nonsynthetic raw materials to develop high performance functional textiles. Common natural materials and some exotic materials such as coir, wool, silk powders, flax and chicken feathers are all considered for developing a variety of advanced textiles. In addition to researching the technical viability of these natural materials, the natural fiber industry is investing human and financial resources to win over the consumers on their environmental benefits, such as biodegradability.
The U.S. cotton industry has effectively used emerging science and technology to reduce environmental burden and energy use. According to Cary, N.C.- based Cotton Inc., a survey conducted among consumers in the U.S., Latin America, China and Europe showed that about 75 percent of people who participated in the survey felt cotton is much safer from an environmental point of view than polyester and rayon. This survey indicates the general mood of consumers about their preference for natural materials and the need to use more of these.
Also, an interesting analysis by Cotton Inc. has shown that in the case of Polo knits, energy consumed is least in the agricultural phase and highest during the textile manufacturing phase. This trend was observed in other end products such as T-shirts and woven-fabric trousers. So, sustainability is not costly at the raw material stage—a positive indicator for the industry to consider different natural and bio-based raw materials.
Nonwoven options
Within the advanced textiles industry, the nonwoven sector is effectively exploiting natural materials. In the case of wipes, unbleached and mechanically cleaned cotton has found its place. TJ Beall Co. has been manufacturing and marketing True Cotton for spunlacing. The company has collaborated extensively with the Nonwovens Research Group at the USDA New Orleans Center to prove the technical viability of greige cotton for use as an alternative to rayon in the spunlacing process.
According Dr. Paul Sawhney, recently retired from the U.S. Dept. of Agriculture (USDA), cotton-based nonwovens can be used as industrial wipes, automotive wipes, oil sorbent, liners in diapers and in incontinence products.
The USDA has focused some attention on hydroentanglement technology with a commercial grade hydroentangling line to undertake a number of projects to enhance the use of cotton in nonwovens. A collaborative project led by Dr. Vince Edwards at the USDA has shown that greige spunlace fabrics can compete against spunbond polypropylene fabrics for use as topsheets in diapers.
In addition to common fibers such as cotton, the industry has been working with fibers such as jute and coir, but these are more focused on developing composites. The Indian jute industry in the West Bengal region of India wants jute to find high performance applications other than just being a packaging material. The Indian Jute Industries’ Research Assoc. has undertaken research on ramie, bamboo and jute blends. Jute- and bamboo-based laminates have been developed for use in the construction and automobile sectors, and the Indian government’s jute research institute, NIRJAFT, has used coir from coconut to develop geotextiles for preventing soil erosion.
Norafin Industries, based in Mülheim, Germany, has been an early pioneer in utilizing flax fibers in nonwovens to develop composite structures as an alternative to glass and carbon fibers.
Byproduct uses
Finding new uses for cotton byproducts such as cotton stalks has occupied researchers at the Mumbai-based Central Institute of Research on Cotton Technology (CIRCOT), since 1979. According to CIRCOT, multiple cotton particle boards are replacing commercial plywood, as they are cheaper and relatively easy to use. Projects at the USDA and Texas Tech University have focused on cotton high-loft structures for acoustic insulation in automobiles. As the automobile sector is highly competitive, cost of natural fiber-based materials may be a barrier for their immediate commercial success.
The South Africa-based Council for Scientific and Industrial Research (CSIR) has developed flame resistant natural fiber-based composites using environmentally friendly FR chemicals for developing composite panels. These panels have met the toxicity and flame retardancy quality standards required by the aerospace industry. CSIR has many interesting projects that focus on sustainable materials for developing advanced textiles, such as flax-based needle-punched fabrics for filtration, composites from soy proteins and chitin-based fibers for biomedical applications, to name a few.
New developments on the horizon
A majority of R&D projects in the industry and academia have focused on developing industrial products. The United Soybean Board (USB), with funding through checkoff dollars from U.S. soybean farmers, supports projects involving soy meal and oil. Soy-based adhesives are finding applications in manufacturing environmentally benign composites.
Prof. Anil Netravali in the College of Human Ecology at Cornell University has been developing advanced composites using green resins from plants for use in applications in buildings, for skate boards and other uses. His work has resulted in green composites from liquid crystalline cellulose, which can have value as an antiballistic material. Dr. Orlando Rojas at North Carolina State University (NCSU), with funding support from the USB, has developed surface finishes from soy protein.
Nanocellulose research and development has occupied researchers in the fiber, pulp and paper industry in the U.S., Scandinavian countries and India, as these materials are finding applications in textiles, cosmetics, pharmaceuticals and electronic industries. The government of India through its Ministry of Agriculture has been investing heavily to develop this field.
CIRCOT has utilized enzymes to degrade waste cotton and linters to develop them into nanocomposites. During April 2015, India unveiled its first pilot nanocellulose plant in Mumbai with a production capacity of 10 kilograms per day.
Green Processing
These days, the textile industry is keen on using environmentally friendly processing methods to reduce the use of energy, water and chemicals. Recently, active collaborations between academia and industry have been flourishing in utilizing plasma technology for creating different surface effects on textiles to develop functional textiles. Prof. Peter Hauser at NCSU has utilized atmospheric plasma to develop fabrics that are hydrophilic on one side and hydrophobic on other side. These selectively finished fabrics could have military applications.
Enercon Industries, Menomonee Falls, Wis., has collaborated with researchers at Texas Tech University in developing breathable polypropylene spunbond fabrics that can find medical applications.
Multiversal Technologies USA, with global headquarters in India, has come up with an improved version of an atmospheric plasma system, which has fragmented electrodes and generates plasma using a dielectric barrier discharge, producing two-dimensional plasma and increasing the productivity of atmospheric plasma systems. According to the company’s CEO, Dr. Krupakar Murali, varying gases imparts different surface effects to textiles; for example, using argon increases surface roughness and oxygen plasma increases “wetability.”
Another technology that has potential, but which has not found wide application yet, is the supercritical carbon dioxide extraction. This technology can be used to develop porous materials by selective extraction to develop ultrafiltration substrates and textiles with improved transport characteristics.
Laser treatments can help with getting different surface textures, and experimentation with carbon dioxide laser treatments have been tried to create different surface textures.
Quo vadis
With sustainability receiving so much attention in different sectors, sustainable raw materials can certainly be exploited for us in green manufacturing processes, and energy conservation methods to develop high performance textiles.
Unlike the commodity textiles industry, which faces stiff competition from Asian markets, industrial textiles as a specialized field will definitely benefit by adapting new and cost-effective technologies. The industry has to borrow tested science from other disciplines such as biology and physics to develop next generation textiles.
This is already happening. But while new and sustainable technologies can have technical viability, from a commercial point of view, they will find immediate adaption in the advanced textiles industry only if they are cost effective. This has to be understood and efforts should be made by the industry and R&D institutions to make sustainable advanced textiles economically viable, too.
Seshadri Ramkumar, Ph.D., FTA (Honorary) is a professor in the Nonwovens & Advanced Materials Laboratory, Texas Tech University.